In this article, we will take you through the comprehensive process we have developed for operating and optimizing reverse osmosis (RO) systems. With Besta’s years of experience and expertise in the water treatment industry, our streamlined approach ensures maximum efficiency, consistent water quality, and sustainable practices. Whether you’re new to RO technology or looking to enhance your current system, this guide will provide valuable insights into our proven methodologies.
Reverse Osmosis Equipment Proceso de filtración
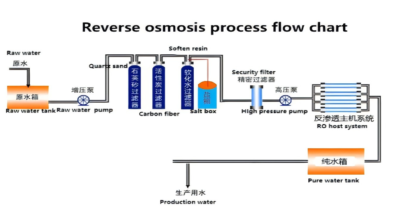
Gráfico de flujo de proceso de ósmosis inversa
- Tanque de agua crudo
The raw water tank stores and buffers incoming water, ensuring a stable and adequate water supply for the entire system. Without a raw water tank, pressure and flow fluctuations during peak usage can disrupt the stability of downstream equipment. Típicamente, the tank’s capacity should be 1 a 1.5 times the system’s water usage or at least enough to provide 15 minutes of operation. A level controller in the tank regulates the opening and closing of the inlet solenoid valve and raw water pump. For instance, when the water level is low, the solenoid valve opens for automatic refilling. Once the water reaches a set high level, the valve stops refilling, and the pump ceases operation when the water level is low. - Bomba de agua cruda
The raw water pump draws water from the tank and boosts the pressure to meet the requirements of subsequent treatment processes. This pump operates in conjunction with the water level sensor in the raw water tank to avoid running dry and causing damage. The pump’s components are made from durable SUS304 stainless steel for long-lasting performance. - Multimedia Filter
The multimedia filter utilizes quartz sand as the filtration medium to remove particulate impurities and suspended solids. When water passes through the filter media, the gaps act as a sieve, trapping particles on the surface. Over time, as the filter surface collects more impurities, the pressure differential across the filter increases, signaling the need for backwashing. Backwashing removes the trapped impurities and restores the filter’s function, ensuring continuous efficient performance. - Filtro de carbono activado
Activated carbon filters rely on the adsorption properties of carbon to remove organic pollutants, microorganismos, cloro, metales pesados, and other contaminants. This process also aids microbial degradation of organic matter, lowering the chemical oxygen demand (BACALAO). This filter also eliminates odors, colors, and synthetic detergents. As a pre-treatment for RO systems, activated carbon filters help prevent organic fouling of RO membranes and remain effective under various temperature, ph, and organic conditions. The filter tank, made from fiberglass-reinforced plastic (FRP), is designed for high strength, corrosion resistance, and a long lifespan. - Filtrante
Softening filters improve the recovery rate of RO systems by preventing scaling due to calcium and magnesium ions. These scales, such as CaCO₃ and CaSO₄, can damage downstream equipment and decrease operational efficiency. The filter uses strong acid cation exchange resin to replace Ca²⁺ and Mg²⁺ with sodium ions. When the resin becomes saturated, regeneration with industrial salt is necessary. The filter’s automatic control system manages the regeneration process, which occurs roughly every 24 hours and includes multiple stages: running, backwashing, regeneration, slow rinse, fast rinse, and refilling the salt tank. This system ensures continuous, effective softening. - Filtro de seguridad
The security filter removes particles larger than 5 µm, preventing them from damaging RO membrane modules or the high-pressure pump. This protection is essential as debris can cause salt leakage and cross-contamination, negatively impacting water quality. The filter operates between 0.2 MPa and 0.5 MPA. When the pressure difference between the inlet and outlet exceeds the set limit, typically 0.05–0.07 MPa, the filter cartridge needs replacing to prevent damage from blockage. - Bomba de alta presión
The high-pressure pump provides the necessary pressure for RO membranes to function. This system uses a top-quality vertical centrifugal pump made from SUS304 stainless steel. The pump is known for its compact design, low noise, low operational costs, y larga vida útil, ensuring reliable and efficient performance. - Ósmosis inversa (RO) Sistema
RO is a pressure-driven process that forces water through a semi-permeable membrane, separating water from solutes. This method reduces the concentration of impurities and improves water purity, achieving desalination rates above 98%. RO systems are effective in treating water of various salinities and offer excellent technical and economic benefits. Although initially limited by cost, recent price reductions have made RO technology widely accessible for desalination and water purification projects. Membranas RO, the core of the system, remove over 98% of water’s ions, bacterias, coloides, and large organic molecules. - Tanque de agua
The water tank stores filtered water, making it available for further use or distribution.
At Besta Membrane Technology, we are committed to delivering state-of-the-art water treatment solutions that cater to diverse needs. Our reverse osmosis equipment process is a result of meticulous research and practical experience, ensuring reliability and performance. By following these steps, you can achieve superior water quality and long-term operational efficiency. If you have any questions or are looking for tailored solutions, our team is here to assist you. Together, let’s make clean water accessible to all!